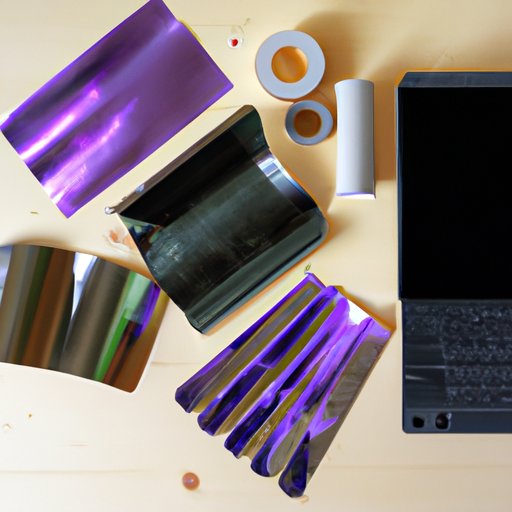
Introduction
If you’ve got a DIY project using aluminum, anodizing is a great way to enhance its durability and appearance. Anodizing aluminum creates a protective layer that resists corrosion and wear, making it ideal for applications such as automotive, construction, and even artificial jewelry manufacturing. In this article, we’ll be exploring how to anodize aluminum step-by-step, including the best tips, common mistakes to avoid, and troubleshooting solutions.
Step-by-Step Guide on How to Anodize Aluminum
Preparing the Surface: Cleaning and Etching
Before anodizing, it’s essential to prepare the surface properly. This involves cleaning and etching the aluminum to remove any impurities and create an even surface for the anodizing process. You can use a commercial aluminum cleaner or a mixture of water and an alkaline solution, such as sodium hydroxide or potassium hydroxide. Then, rinse the aluminum with water and scrub it with a scouring pad or stainless steel brush to remove any remaining dirt or oils on the surface.
Next, etch the aluminum. This step is essential to create a rough surface that the anodizing layer can grip to, allowing it to become thicker and more durable. You can use an aluminum-specific etching solution, such as hydrofluoric acid, or a mixture of water and a strong acid, such as phosphoric or sulfuric acid. Make sure to follow the manufacturer’s instructions carefully and use protective equipment such as gloves, goggles, and a respirator when handling these chemicals. Rinse with water thoroughly afterward.
Anodizing the Aluminum: Setting Up the Anodizing Bath and Applying
During this step, we’ll set up the anodizing bath and apply the anodizing layer. To create the anodizing bath, you’ll need an electrolyte solution such as sulfuric acid and distilled water. You can use a premixed solution or prepare the solution using industrial chemicals, but always ensure that it’s at the right concentration and temperature. The recommended concentration of sulfuric acid in your solution is 10 to 12%. Keep in mind that you will have to control the quality of the electrolyte solution for consistent finishing results.
Bear in mind to wear protective clothing and goggles as well.
Next, we’ll submerge the prepared and cleaned aluminum material in the electrolyte for the anodization process. The anodizing will create a porous layer on the aluminum surface, where electricity passes through the electrolyte and aluminum, and oxygen molecules form on the surface, building up the anodized layer.
Dying the Aluminum: Application and Options
After the anodizing process is complete, you can dye the aluminum to achieve a vibrant color or a unique look. There are several options with dyes, including acid, reactive, and organic dyes. Consider the type of metal you’re working with and the color you want to achieve when deciding on the right dye. We recommend working with a dye made specifically for use with anodized aluminum and following the manufacturer’s instructions carefully.
Some colors will require a second dyeing process to achieve vibrancy, and others can only be achieved through the use of organic dyes.
Sealing the Aluminum: Different Methods of Sealing and Drying
The final step of anodizing aluminum involves sealing the anodized layer. This helps to ensure the layer is more corrosion resistant, wear-resistant, and less likely to fade over time. There are different methods of sealing, depending on your project and preferences. A few options include boiling aluminum parts in hot water or using a sealant, such as nickel acetate, to form a barrier on the surface of the aluminum.
After the sealing process, allow the aluminum to dry, and you’ve got an anodized aluminum product that is both durable and stylish.
Tips for Achieving the Best Color and Finish When Anodizing Aluminum
Choosing the Right Dye: Acid, Reactive, and Organic Dyes
The type of dye you choose will depend on the color you want to achieve. Acid dyes are ideal for achieving bright, vibrant shades, reactive dyes for more color options on specialized metal surfaces, while organic dyes are the most cost-effective.
Preparing the Surface: Proper Cleaning and Masking
Ensure all surfaces of the aluminum are precisely clean, and areas you do not want to be anodized should be masked off.
Controlling the Anodizing Bath: Concentration, Temperature, and Quality of Electrolyte
Anodizing baths need to be of high quality, and a lower concentration may not produce the desired effect or even corrode the metal. Higher concentration can lead to over-anodization or incomplete dying. Keeping the right temperature and providing the right amount of energy is also crucial.
Consistency in Quality: Maintaining the Equipment and Re-coating When Necessary
To maintain the consistency of the anodized layer, appropriate equipment should be used, and re-coating provided when necessary.
Common Mistakes to Avoid When Anodizing Aluminum
Inadequate Cleaning or Preparation of the Surface
Anodizing the aluminum material without proper cleaning can lead to discoloration, dipped joints, and other surface imperfections.
Over-anodizing the Material or Using an Incorrect Electrolyte Concentration
Over-anodizing the metal leaves it prone to fading and wear issues. Using an incorrect electrolyte concentration will also lead to corrosion.
Not Rinsing and Neutralizing the Treated Surface
Not cleaning the aluminum material carefully after anodizing or leaving any excess residue can greatly affect the appearance in the end.
Overheating the Solution or Under-Supporting the Aluminium during the Process
Under-supporting the aluminum part or overheating the solution can cause cracking or splitting of the surface, which immediately ruins the result.
The Pros and Cons of Anodizing Aluminum Compared to Other Finishing Options
Advantages of Anodizing: Enhanced Corrosion and Wear Resistance, Electrically Non-Conductive, Longer Lifespan and Vibrant Color Options
Anodizing aluminum is far superior to powder coatings. It makes the surface highly resistant to wear and corrosion, non-conductive, which makes it useful for specialized electronics, pharmaceutical, food processing industry, as well as increasing longevity.
Disadvantages of Anodizing: Color Fading, Costly, and Labor Intensive
Anodized aluminum is colorfast and fade-resistant. However, prolonged exposure to UV light and heat will eventually cause fading and discoloration. The process is costly and takes long, but the end product is worth the investment.
Real-World Examples of Anodized Aluminum Projects
Different colors and finish types could be obtained through anodization. You can achieve metallic and matte finishes or vibrant colors with a reflective sheen. It is ideal for resisting corrosion, which makes it fit for use on artificial jewelry manufacturing, which does not fade or peel off. It’s also common in construction and automotive industries where durability and vibrant colors are needed.
Troubleshooting Common Issues Encountered When Anodizing Aluminum
Uneven Coloring and Fading of Color
This is often the result of the inadequate preparation of the surface, inconsistent anodizing baths, or prolonged exposures to UV light and high temperatures. It can be remedied by re-cleaning, re-anodizing, or coating over the anodized surface.
Adhesion Problems of Dyes and/or Sealant Layer
This happens when surface preparation is not adequate or when the surface that’s to be anodized is dirty. Cleaning and resealing the surface should solve the problem.
Surface Cracking or Splitting
This is often the result of under-supporting the aluminum part during the anodizing process or overheating the solution. Making sure to follow all procedures and instructions will likely prevent this.
Conclusion
We hope you’ve found this guide informative and helpful in your aluminum anodizing projects. By providing a clean surface, an adequate electrolyte solution, the right temperature, and using the correct equipment and techniques, anyone can achieve long-lasting, vibrant anodized aluminum finishes for all their projects. Remember to always take safety precautions and to follow the manufacturer’s instructions carefully, and you’ll be anodizing aluminum like a pro in no time.