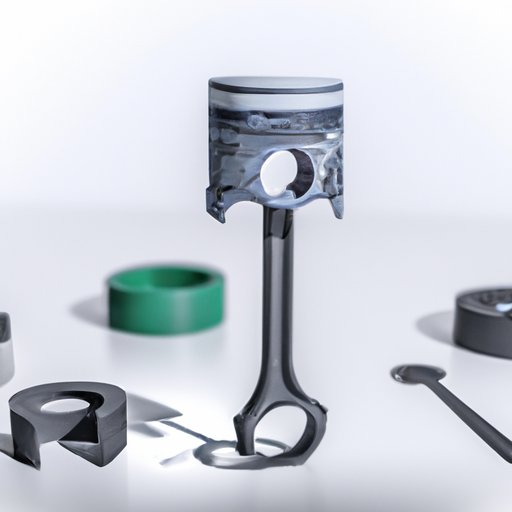
I. Introduction
Making your own piston may seem like an overwhelming task, but with the right resources and knowledge, it can be a rewarding and cost-effective solution for many mechanical applications. This article will provide a comprehensive guide to crafting your own piston, covering traditional manufacturing methods, 3D printing options, and creative DIY solutions. We’ll also explore the importance of piston design and share tips for making high-performance modifications.
II. Step-by-Step Guide on How to Make a Piston
To make a piston from scratch, you’ll need access to specialized machinery, materials, and tools. The process can be broken down into several basic steps:
- Casting: Create a mold of the desired piston shape in sand or ceramic, then pour in molten metal. Allow the metal to cool and solidify before removing the casting from the mold.
- Grinding: Use a surface grinder to smooth out the rough surface of the casting. This step is important for ensuring that the piston fits securely and moves smoothly within the engine.
- Polishing: Polish the piston using a rotary buffer to achieve a high shine. This step is primarily cosmetic but can also help to increase the piston’s lifespan.
- Assembly: Finally, assemble the piston with other engine components, such as connecting rods and rings, according to the manufacturer’s specifications.
It’s important to note that this process requires specialized knowledge and equipment. If you’re not comfortable with any of the steps involved, don’t hesitate to seek help from an expert.
III. Using a 3D Printer to Make a Piston
3D printing has revolutionized the manufacturing industry, allowing for greater precision and customization at a lower cost. To make a piston using a 3D printer, you’ll first need to design the piston using CAD software. Once you have the design, you can send it to a 3D printer and watch as the machine creates the piston from layers of materials such as metal or plastic.
While 3D printing can simplify the manufacturing process, it’s important to note that the technology is still evolving. Not all 3D printers are capable of producing high-quality pistons, and some materials may not be strong enough for certain applications. As with any manufacturing process, it’s important to research and consult experts in the field before attempting to make a 3D-printed piston.
IV. DIY Solutions for Making a Piston
If you don’t have access to traditional machinery or a 3D printer, there are still several DIY solutions for making a piston. For example, you can use a lathe machine to turn down a pre-made piece of metal to the desired shape, or you can weld together several metal plates to create the piston structure.
Keep in mind that these DIY solutions may not be as precise or durable as traditional manufacturing methods or 3D printing. It’s important to test the piston thoroughly before using it in a high-stakes application.
V. The Importance of Piston Design
The design of a piston can greatly affect its performance and lifespan. Different materials, shapes, and coatings can be used to increase strength, reduce friction, and keep the piston running smoothly. When designing a piston, it’s important to consider factors such as the intended use, engine type, and budget.
For example, a high-performance racing piston may be designed with aircraft-grade aluminum and coated with a ceramic material to increase durability and horsepower. A piston for a stationary industrial application, on the other hand, may be designed with cast iron or steel to withstand heavy usage and extreme temperatures.
VI. The Cost of Making Pistons
Making your own piston can be a cost-effective solution for many applications, but it’s important to weigh the costs against the potential benefits. Traditional manufacturing methods require specialized machinery and materials, which can be expensive to purchase or rent. 3D printing can be a more affordable option, but the upfront cost of a quality machine and materials can still be significant.
If cost is a concern, consider alternative materials or creative DIY solutions. For example, a piston can be made from a ceramic material instead of metal, or a pre-made piston can be modified to fit a specific application. It’s important to remember that cutting costs may also mean sacrificing quality or durability.
VII. How to Fix or Replace a Piston
Even the best-made pistons can experience issues, such as broken rings, burnt or cracked heads, or bent connecting rods. In some cases, these issues can be fixed by repairing or replacing the damaged parts. In other cases, a full piston replacement may be necessary.
If you’re experiencing issues with your piston, it’s important to troubleshoot the problem and identify the root cause. Attempting to repair or replace a piston without the knowledge or experience can be dangerous and may cause further damage to the engine.
VIII. Tips for Making High-Performance Pistons
Making a high-performance piston requires specialized knowledge and tools. Techniques such as cryogenic processing and electrodeposition can be used to increase strength and durability. Materials such as titanium and ceramic can also be used to create a high-performance piston.
If you’re interested in making high-performance modifications to your piston, it’s important to research and consult experts in the field. Attempting these modifications without the proper knowledge and equipment can be dangerous and may cause irreparable damage to the engine.
IX. Conclusion
Making your own piston can be a rewarding and cost-effective solution for many mechanical applications. Whether you choose traditional manufacturing methods, 3D printing, or creative DIY solutions, it’s important to consider the design, cost, and potential benefits of your piston before attempting to make it. Remember to seek out expert advice and guidance when needed, and always prioritize safety when working with machinery and tools.