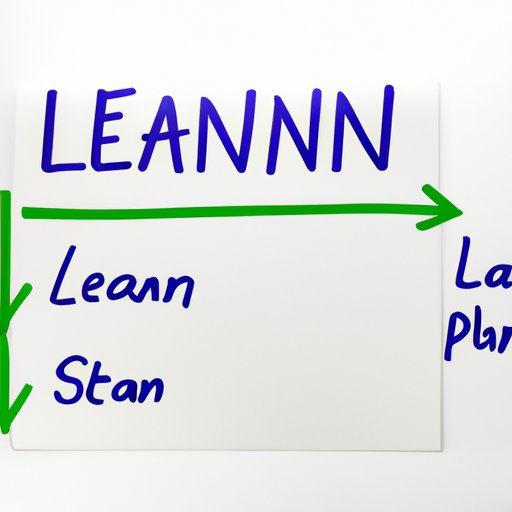
I. Introduction
Have you ever heard of lean management? It’s a concept that emphasizes reducing waste and maximizing value in business operations. With the constant pressure to increase productivity and efficiency while reducing costs, lean management has become an increasingly popular approach to streamlining processes and improving profitability. In this article, we’ll explore what lean management is, why it’s important, and how you can get started implementing it in your own business.
A. Explanation of the Concept of Lean Management
Lean management is a systematic approach to identifying and eliminating waste in business operations while maximizing value to the customer. It originated in the Japanese manufacturing industry, where companies like Toyota used it to improve efficiency, quality, and customer satisfaction. Today, lean management principles have been applied to a wide range of businesses, from manufacturing to healthcare to government services.
B. Importance of Lean Management for Businesses
Businesses are under constant pressure to improve their operations while reducing costs and increasing profitability. Lean management provides a framework for achieving those goals by streamlining processes, reducing waste, and increasing efficiency. With lean management, businesses can improve productivity, quality, and customer satisfaction while reducing costs and improving profitability.
C. Purpose of the Article: To Help Readers Solve the Problem
The purpose of this article is to provide a comprehensive guide to lean management, from the core principles to real-world examples to step-by-step tips for implementation. Whether you’re a business owner, manager, or employee, you’ll find valuable insights and strategies for improving your organization’s operations and achieving your goals.
II. Core Principles of Lean Management
Before we dive into real-world examples and tips for implementation, let’s define the key principles of lean management.
A. Defining the Key Principles of Lean Management
The five core principles of lean management, as defined by the Lean Enterprise Institute, are:
- Value: identify the value that your customers place on your product or service
- Value Stream: map out the value stream to identify all of the processes involved in delivering the product or service
- Flow: design a flow of products or services that is continuous and smooth
- Pull: produce only what is needed, based on customer demand
- Perfection: strive for continuous improvement in all aspects of the business
B. Explanation of How These Principles Enhance Business Operations
By focusing on these core principles, businesses can identify and eliminate waste, increase efficiency, and improve the quality of their products or services. By understanding the value that customers place on their products or services, businesses can design processes that deliver that value while minimizing waste. By mapping out the value stream and designing a continuous flow, businesses can reduce lead times and increase efficiency. By producing only what is needed based on customer demand, businesses can reduce inventory and improve responsiveness. And by striving for continuous improvement, businesses can adapt and improve their operations over time.
III. Real-World Examples of Lean Management
Now that we’ve defined the core principles of lean management, let’s look at some real-world examples of companies that successfully use lean management.
A. Examples of Companies That Successfully Use Lean Management
One example of a company that successfully uses lean management is Toyota. In the 1970s, Toyota developed a production system known as the Toyota Production System, which became the foundation for modern lean management. The system emphasizes continuous improvement, waste reduction, and quality control, and has been widely adopted by other companies around the world. Another example is Amazon, which uses lean management principles in its fulfillment centers to reduce waste and increase efficiency.
B. Explanation of How These Companies Have Benefited from Implementing Lean Management
Companies that implement lean management can benefit in a number of ways, including:
- Reduced waste: by identifying and eliminating waste, businesses can reduce costs and increase profitability
- Improved efficiency: by streamlining processes and reducing lead times, businesses can increase productivity and responsiveness
- Improved quality: by focusing on customer value and continuous improvement, businesses can improve the quality of their products or services
- Increased employee engagement: by involving employees in the identification and elimination of waste, businesses can improve employee satisfaction and engagement
C. Lessons That Readers Can Learn from These Examples
The key lesson that readers can learn from these examples is that lean management is a proven approach to improving business operations. By focusing on the core principles of value, value stream, flow, pull, and perfection, businesses can reduce waste, increase efficiency, and improve profitability.
IV. Advantages of Implementing Lean Management in Your Business
Now that we’ve looked at real-world examples of lean management, let’s explore some of the key advantages of implementing lean management in your own business.
A. Explanation of the Main Benefits of Lean Management for Businesses
Some of the main benefits of lean management for businesses include:
- Reduced costs: by identifying and eliminating waste, businesses can reduce costs and increase profitability
- Increased efficiency: by streamlining processes and reducing lead times, businesses can increase productivity and responsiveness
- Improved quality: by focusing on customer value and continuous improvement, businesses can improve the quality of their products or services
- Improved customer satisfaction: by delivering value to customers and improving the quality of products or services, businesses can improve customer satisfaction and loyalty
B. How Lean Management Can Improve Productivity, Efficiency, and Profitability
By reducing waste and increasing efficiency, lean management can improve productivity and profitability. By focusing on customer value and improving the quality of products or services, lean management can improve customer satisfaction and loyalty. And by involving employees in the identification and elimination of waste, lean management can improve employee satisfaction and engagement.
C. The Importance of Identifying Business Goals for Effective Implementation
Before implementing lean management, it’s important to identify the business goals that you want to achieve. Whether you’re looking to reduce costs, increase efficiency, improve quality, or all of the above, it’s important to have a clear understanding of what you want to achieve and how lean management can help you get there.
V. Getting Started with Lean Management: Step-by-Step Guide
Now that we understand the core principles and benefits of lean management, let’s explore some tips for getting started with lean management.
A. Tips on How to Get Started with Lean Management
Some tips for getting started with lean management include:
- Identify your business goals and define the metrics that you’ll use to measure progress
- Map out your value stream and identify areas of waste
- Develop a plan to eliminate waste and improve efficiency
- Involve employees in the process and provide training as needed
- Measure progress and adjust your plan as needed
B. Identification of Key Areas to Focus on When Implementing Lean Management
When implementing lean management, it’s important to focus on key areas such as:
- Process flow: design a flow of products or services that is continuous and smooth
- Inventory management: reduce inventory and produce only what is needed based on customer demand
- Lead time reduction: identify and eliminate bottlenecks in the value stream
- Standardization: establish standard processes and procedures to reduce variation and improve quality
C. Explanation of How to Measure Progress and Success
To measure progress and success with lean management, it’s important to define metrics that align with your business goals. Some metrics to consider include:
- Cycle time: the time it takes to complete a process from start to finish
- Throughput: the amount of product or service that can be produced in a given period of time
- Inventory levels: the amount of inventory on hand at any given time
- Customer satisfaction: the degree to which customers are satisfied with your products or services
VI. Challenges in Implementing Lean Management and How to Overcome Them
While there are many benefits to implementing lean management, there are also some common challenges that businesses can face.
A. Common Obstacles Businesses Face When Implementing Lean Management
Some common obstacles businesses face when implementing lean management include:
- Resistance to change: employees may be resistant to changes in processes or procedures
- Difficulty identifying waste: it can be challenging to identify all of the areas of waste in business operations
- Need for ongoing training: employees may need ongoing training to effectively implement lean management
B. Strategies to Overcome These Obstacles
Strategies for overcoming these obstacles include:
- Communication: communicate the benefits of lean management to employees and involve them in the process
- Training: provide training and coaching to employees to help them understand and implement lean management principles
- Continuous improvement: focus on continuous improvement and adaptability to address ongoing challenges
C. Importance of Continuous Improvement and Adaptability in Lean Management Implementation
Continuous improvement and adaptability are key to successfully implementing lean management. By continuously evaluating and refining processes, businesses can continue to improve efficiency and reduce waste. By remaining adaptable and open to change, businesses can respond to new challenges and opportunities as they arise.
VII. Conclusion
Lean management is a powerful approach to streamlining business operations and improving profitability. By focusing on core principles such as value, value stream, flow, pull, and perfection, businesses can reduce waste, increase efficiency, and improve customer satisfaction. While there are challenges to implementing lean management, there are also strategies for overcoming them. By following a step-by-step process and focusing on key areas such as process flow, inventory management, and lead time reduction, businesses can achieve their goals and improve their operations. So why not start implementing lean management today and see the benefits for yourself?
A. Recap of the Main Points of the Article
In this article, we explored what lean management is, why it’s important, and how to implement it in your business. We defined the core principles of lean management, looked at real-world examples of companies that successfully use lean management, and explored the benefits of implementing lean management in your business. We provided step-by-step tips for getting started with lean management, identified common obstacles businesses face when implementing lean management, and provided strategies for overcoming those obstacles.
B. Encouragement to Readers to Implement Lean Management
We encourage readers to start implementing lean management in their own businesses to improve productivity, efficiency, and profitability. By following the core principles and focusing on key areas such as process flow, inventory management, and lead time reduction, businesses can achieve their goals and improve their operations.
C. Call to Action for Readers to Share Their Success Stories or Ask Questions
We would love to hear from readers who have successfully implemented lean management in their businesses. Please share your success stories or ask any questions you may have in the comments below.